Rock40
Active Member
I've complained about the welds on this 715 before. Now I'm going to show you some horrible proof.....
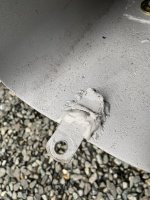
Dear goodness. This one didn't receive ENOUGH booger weld, probably why it broke.
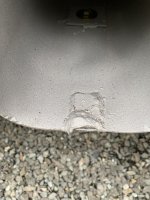
This was probably a jerry can mount gone totally sideways... please appreciate the far from round torched out hole. Nobody ever bothered to even clean up the slag. Right on the side of the bed too
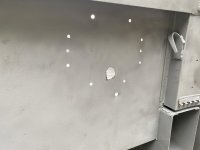
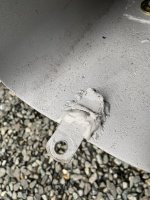
Dear goodness. This one didn't receive ENOUGH booger weld, probably why it broke.
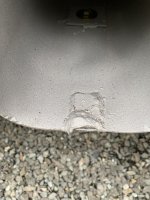
This was probably a jerry can mount gone totally sideways... please appreciate the far from round torched out hole. Nobody ever bothered to even clean up the slag. Right on the side of the bed too
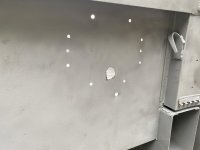
Last edited: